Can DFIs spark a 3D-printing revolution in critical infrastructure?
Uxolo talks to the UK’s development financier, CDC Group, about a pioneering collaboration with Holcim in Malawi that has inaugurated the world’s first 3D-printed school.
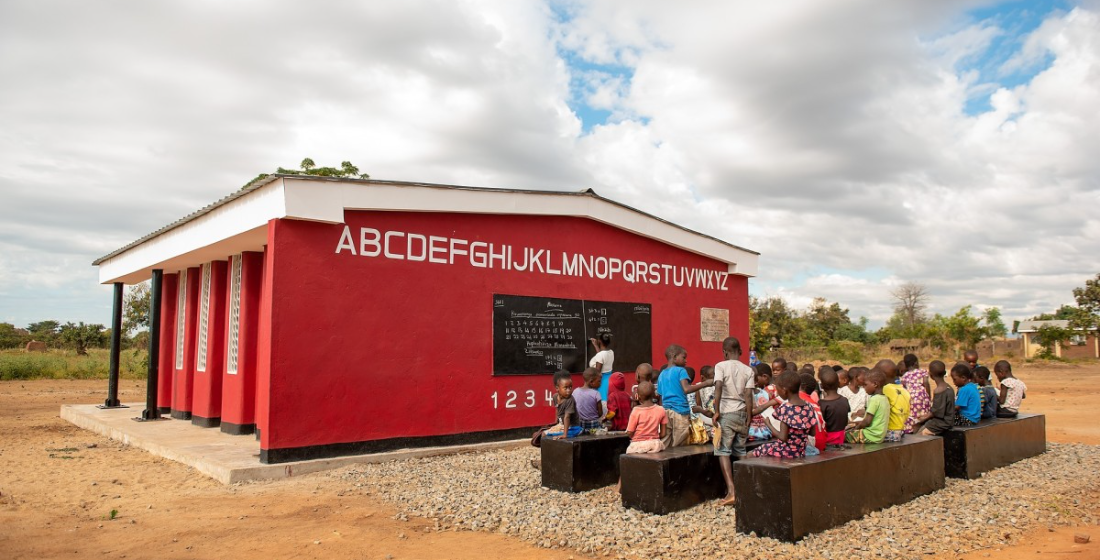
Last month, 14Trees, a joint-venture between UK development finance institution CDC Group and Swiss sustainable building firm Holcim, announced the creation of the world’s first 3D-printed school. The school was built in the Salima district of central Malawi, and its walls were printed in just 18 hours—compared to several days with conventional building materials.
Children of the Kalonga village community began learning in their new school on 21 June. Made of concrete placed layer by layer through a computer-controlled nozzle, the school is made up of a single room with rounded corners and is big enough to accommodate 50 students.
The school demonstrates that 3D printing can play a key role in bridging the world’s education infrastructure gap by building high-quality classrooms for children in a sustainable, affordable and fast-paced manner at scale. In Malawi alone, UNICEF estimates there to be a shortage of 36,000 classrooms, which would take 70 years to build using conventional methods. According to 14Trees, that infrastructure gap could be bridged in just 10 years with 3D printing.
The 3D-printing process significantly reduces the time, cost and materials used for building not only schools but also housing as well, while reducing their environmental footprint by more than 50% compared to conventional methods. In addition to the school in Salima, 14Trees also built its first 3D-printed prototype house in Lilongwe, Malawi in just 12 hours, compared to almost four days using conventional methods. The company is now looking to scale out the technology across the broader region, with projects already in the pipeline in Kenya and Zimbabwe.
Uxolo caught up with Abhinav Sinha, CDC’s head of manufacturing and co-head of technology, to discuss the ground-breaking project and to find out what development financiers can do to catalyse the 3D-printing revolution in critical education and housing infrastructure.
Uxolo: How can 3D printing help narrow the developing world’s critical infrastructure gap?
Abhinav Sinha: 3D printing is revolutionising approaches to design and manufacturing across various industries. The innovation creates a valuable opportunity to deliver a rapid and economical approach to construction for many uses, notably affordable housing and education provision. The benefit of deploying 3D printing for construction is clear in developing countries where governments face mounting housing crises, and where achieving universal primary and secondary education enrolment remains a high priority in national development agendas. The development impact and commercial value that this technology can achieve is transformational and indeed compelling.
The ink used to print the walls of this new school is now manufactured in Malawi; however, it was initially imported because robust local supply chains had yet to be developed. Manufacturing the ink within the countries where the buildings are being constructed presents an opportunity to significantly lower the cost. This brings benefits to buyers, who typically have financial constraints. Furthermore, investment in operations that upskill locally based and indigenous operators of the 3D printing machinery will also position the new technology as a catalytic force for job creation, given the employment opportunities in the manufacturing process.
How did the collaboration between CDC and Holcim come about?
Holcim began its affordable housing unit in 2011, intending to develop innovative products and solutions that address the lack of low-cost housing in mature and emerging markets. As part of this development, a new product was prototyped, the soil-stabilising brick (SSB) called Durabric, which has now been tested through this pilot in Malawi. Durabric provides a solution to rapid deforestation, a problem faced by many developing countries, which happens as a result of using clay burnt bricks as a primary building material.
Holcim initially engaged CDC by requesting an introduction from the UK's Department for International Development (DFID) to explore collaboration. It became clear that CDC could contribute patient and long-term capital to support the product launch and further innovation.
Our subsequent collaboration now enables 14Trees to commercialise innovative green building solutions at scale in sub-Saharan Africa and beyond.
How was the project financed?
CDC and Holcim jointly committed $10 million to the joint venture, with CDC contributing the $5 million equity investment through our Impact Accelerator strategy. CDC’s Impact Accelerator focuses on investments which have potential to be commercially sustainable but involve risks that are too high, or where the return may be too low, to attract commercial investors. By reaching the underserved or investing in pioneering technology, CDC’s investments have a catalysing effect on the market and can help to attract greater commercial capital.
Were there any challenges you encountered on the way?
Until the pilot projects had come to fruition in Malawi, most 3D-printed projects were restricted to controlled environments such as research centres, where all parameters such as temperature or humidity levels are under constant surveillance and control. Therefore this innovation in Malawi is rare. Nevertheless, 14Trees overcame the associated hurdles and infrastructure deficits expected when building in remote environments with limited access to electricity and water, in addition to the unpredictable nature of high temperatures and strong winds. Without the close collaboration, shared insight and intimate knowledge of the on-ground Malawian team that are fully trained to operate the 3D printer, the development would not have been a success.
How is this method so much more environmentally friendly than traditional methods? Isn’t concrete meant to have a large carbon footprint?
The blend of air, sand, gravel, cement and water create concrete. Cement is one of the key ingredients in concrete, which is extensively relied on around the globe by engineers, developers, and builders in construction. However, it is precisely the chemical and thermal process of cement production that is a major cause of carbon dioxide (CO2) emissions. According to think tank Chatham House, more than four billion tonnes of cement are produced annually, accounting for approximately 8% of global CO2 emissions. So cement is a significant contributor to climate change.
Building with 3D printing in Malawi significantly reduces CO2 emissions by up to 70% compared to building with burnt bricks—the conventional construction method widely deployed across the country. Holcim's Innovation Centre performed a life cycle assessment to examine the effects of the construction process on the environment to be certain that the 14Trees approach would serve as a better solution for the environment. Holcim found that a 3D-printed house emits 70% less CO2 than a conventionally built home, whereas a 3D-printed school emits 50% less CO2 than a school built by typical construction methods.
CO2 emission levels vary by country and the building method being measured against; however, no matter where the location or the construction method that’s examined, it’s evident that 3D printing consumes fewer materials than conventional construction methods. During the 3D printing construction process, the machinery collects a precise amount of cement each time it deposits—this contributes to how 3D printing is considered a green and clean solution for the environment. Due to its controlled consumption and construction of walls with minimal density, 3D printing lowers material waste and CO2 emissions.
In line with the Paris Agreement, 14Trees has been exploring avenues where innovation with materials can reduce the environmental impact of cement production; for example, identifying natural fibres and recycled concrete as valuable components for environmentally conscious construction. Holcim has also developed a zero-carbon concrete. These innovations provide possibilities to produce a range of materials that could be fortified and sourced locally in the countries identified for 14Trees' expansion strategy. These developments are fundamental to reducing construction costs meaningfully, and this helps serve consumers with a life-changing accommodation or education need while positively contributing to the atmosphere.
Can you elaborate on the projects you have in the pipeline in Kenya and Zimbabwe, and your longer-term ambitions for 14Trees?
14Trees has demonstrated the potential for 3D printing in Africa and offers a clear roadmap for further developing the technology.
Following the reception of the pilot projects in Malawi, we are exploring collaboration with partners from the development finance community, private sector, non-governmental organisations, and public sector in countries across the continent. CDC’s long-term mission is to support the supply, build on this pioneering technology, and enhance its potential to significantly improve the quality of life for communities in CDC’s focus countries. For the housing sector, our goal is simple: to benefit as many households as possible through improved access to work and infrastructure. In this, we are excited to help provide a potential vehicle that can eventually enable safe, well-located, and reliable home-ownership.
We also expect the size and design of the 3D-printed constructions to evolve to accommodate the changing lifestyles and functional needs of the consumers over time. For context, the housing deficit in sub-Saharan Africa is estimated at 50 million units. And over 40,000 people move to African cities each day—many of whom migrate across borders or from rural to urban areas, searching for economic opportunities, despite the lack of housing for many upon arrival. Inability to access housing impedes development as it restricts access to employment, financial services, basic security, and essential health and social services. So we are committed to focusing our investment on innovative technology that will rapidly accelerate the supply of affordable homes.
14Trees has a robust pipeline of projects in schools and affordable housing in Malawi, Zimbabwe and Kenya. It has been working in Malawi to produce soil-stabilised bricks (Durabric) on a mass scale. Developments of housing projects in Kenya and Zimbabwe are going to begin soon, which we aim to bring to the market this autumn.
The homes that we will be 3D printing in Kenya and Zimbabwe will be purpose-built and seek to provide favourable living conditions for overcrowded and poorly serviced informal settlements with substandard utilities, such as lack of running water, sewage issues or inconsistent electricity supply. 14Trees will also be printing a school in Madagascar, and we are progressing with projects in Western Africa, in Nigeria especially—contributing to the supply of housing in Africa’s most populous nation, where there is a rising need.
Will this world-first project help speed up the 3D-printing revolution in education and housing infrastructure?
The call for affordable and environmentally friendly construction is urgent, not only in Malawi but across the continent. The economic consequences of climate change in the form of erosion, floods and natural disasters reveal the salience of climate resilient infrastructure and housing in Africa and beyond.
3D printing for construction is still a nascent industry and we have partnered with multiple stakeholders to work on several aspects of the innovation to bring this solution to the market—setting ambitious targets to prove the efficacy of the technology across Africa over the next 12 to 18 months and to reach at least 10-20% lower cost than conventional methods. The other key advantage of this technology is speed at scale, which can help address chronic shortages quickly and we have demonstrated that in our projects in Malawi.
Our overarching objective is to increase its scalability, which will spark a much-needed revolution in construction, whether in Kenya, where the housing shortage is estimated at 2 million units; or in Nigeria, where there remains a shortage of 17 million units for the growing number of underserved communities. As part of our strategy to bring a breakthrough solution to the market, we are advocating for best practices in 3D printing construction in Africa. We are currently prioritising these efforts, which involve rigorous testing. It also requires engagement with beneficiaries' needs in various climates and conditions, as we strive to establish the guiding principles for 3D construction with regulators and partners in the construction, housing and urban planning sectors.
How can the development finance community help catalyse this 3D-printing transition?
On the supply side—particularly in Africa’s nascent housing market—there is a need to develop housing data, industry benchmarks and a strong track record of completed projects that will attract capital to bring more constructions to the market. There is a unique opportunity for the development finance community, commercial investors, developers, governments and education institutions to lead research and development into new materials that can advance development of 3D printing within the construction sector.
Progressive equity investments, grants, and guarantees for 3D printing machinery can de-risk projects and mobilise more considerable sums of capital for investment in projects where commercial sources are not ready to front the majority of the cost—accelerating the scalability of 3D printed construction in the process.